Reduce Stockouts
Maintaining on-shelf availability is blend of art and science. Getting it right is extremely difficult. Getting it wrong is very costly.
According to ECR Europe, on-shelf availability is extremely important to customers, but despite all of the investment in supply chain and stock management systems, new measuring and monitoring protocols, and even AI assisted inventory predictions, stockouts remain stubbornly persistent.
A simple cost calculation multiplies the unit price of the unavailable item with its average sales volume and time out of stock, so the cost of not having a $10 pack of detergent that would normally sell 10 units is $100 per day.
A better model would also factor in the staff hours required to identify and remedy the situation, although this can be extremely difficult to measure accurately. Then there are more complex factors to take into account, such as whether a customer selects a substitute product or the sale is lost entirely, and the damage to brand perception and therefore loyalty.
One way of thinking about on-shelf availability and out-of-stocks, is that gaps on shelves correspond to gaps in systems, caused either by inaccurate data or inefficient measurement. The market is awash with complex technological solutions targeted at filling these gaps, ranging from huge sensor-packed robots slowly roaming the aisles, to mobile device apps that process pictures of shelves.
These kinds of solutions provide a better picture of on-shelf inventory levels, but they have shortcomings themselves. The most obvious issue is that they add another layer of cost. There is obviously a trade-off between the CAPEX heavy robotic solutions and the OPEX heavy option of having store staff patrol the aisles with an app on a mobile device, but the bottom-line effect is largely the same.
Another major issue is that the robots or apps are only measuring while they are on the shop floor, and they cannot be around for every minute of a day’s trading hours. If a team of shoplifters cleared an entire category, for instance, these systems would be unaware until they next time they are deployed. Every second is valuable in these scenarios, particularly as highly targeted categories such as large packs of detergent, baby formula, or fresh meat also tend to be high value items and high volume sellers .
The SAI Approach
SAI takes a different approach - one that is always available, always aware, and that is even suitable for stores with the leanest staffing models. Using existing CCTV camera feeds, our highly accurate computer vision algorithms recognise the very second that the last item is taken from a shelf. Instant alerts are then sent to store staff who can take immediate action, turning a process that could take many staff-hours every day into one that takes up only a few minutes. We can also bring the process forward, alerting to low-stock levels before they become costly stockouts.
On top of this, the SAI platform is also tuned to detect shoplifting and other loss generating events, so that security officers are aware of shelf-clearing well before thieves attempt to leave the store.
Come and see the system in action at NRF’s Big Show in January, or book a demo.
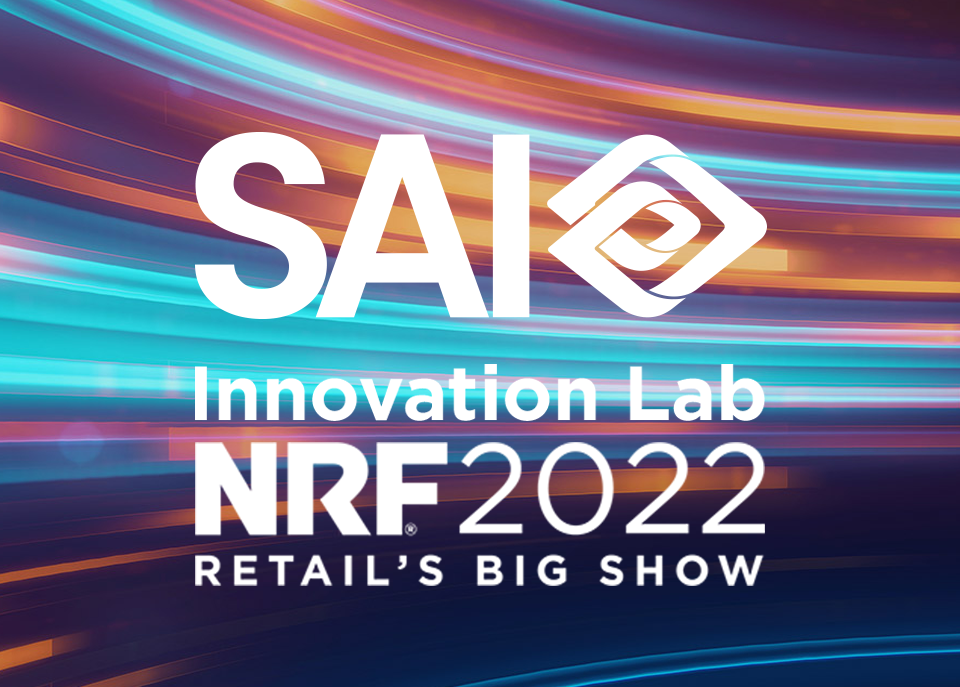